It’s a case of David versus Goliath. A tiny, privately held Rocklin company is taking on multimillion-dollar competitors with a lightning-fast technology that’s more sophisticated than the competition’s.
Charles “Chip” Gracey III, founder of Parallax Inc., is the sole designer of the Propeller 1 and Propeller 2 multicore microcontroller chips — computer chips with multiple built-in processors that can be programmed to perform eight operations at once. In a factory setting, for example, the chip could monitor temperature, water and pump pressure levels, measure output and more.
It’s unheard of for an individual to single-handedly design a chip in the computer electronics industry, which typically relies on teams of brainiacs to achieve such feats. At large companies such as Intel Corp. or Atmel Corp., teams of 40 to 50 engineers would collaborate to develop these chips.
“He’s a genius,” says engineering manager Jessica Eulman. “And what’s so amazing is he is self-taught.”
Aiming to compete with large chip manufacturers Atmel and ARM, Gracey in 2006 developed the versatile Propeller 1, a powerful multiprocessor chip with audio capability. Later this year, Parallax would unveil Propeller 2, which runs nine times faster than its predecessor and can generate high-definition video. Because both Propeller chips can run tasks simultaneously, they can replace several chips, reducing costs and increasing productivity.
“This is the product that is going to move Parallax from $9.5 million in annual gross revenue to $15 million in the next three years,” says Ken Gracey, president of Parallax and Chip’s younger brother.
Parallax has so far sold 1 million chips, they’re distributed in 41 countries worldwide and the company’s goal is to dramatically boost the number of chips sold as more consumers discover their versatility.
“The applications are varied and really diverse, so the possibilities are endless,” Eulman says. “We have an incredible opportunity to gain a foothold in some of these markets that have been dominated by outdated and more expensive applications.”
Parallax’s chips can be used in solar panels to track the location of the sun for more efficiency, run complex robots, operate medical machines or to monitor controls in a factory.
In 2001, Parallax’s gross revenue was $6 million, climbing since then to the current $9.5 million. Still, growth has been slower than anticipated, but business is finally revving up as more companies are building Propeller 1 into products used for robotics, renewable energy, medical applications and energy management.
Company sales have increased 50 percent in the past decade and have continued to grow consistently since Propeller 1’s debut. The company is still trying to change a perception that it is a small player making robots and microcontrollers for the hobby and education industries because, while it does that, the bigger plan is to conquer the overall microcontroller chip manufacturing market.
A year ago, the Gracey brothers launched Parallax Semiconductor to promote and sell their chips. In forming a separate division for the microcontrollers, Parallax’s message to the industry is clear: We will be a serious contender in the microcontroller chip field.
“My inspiration was to design a chip exactly as I wanted it,” says Chip Gracey, now the director of research and development. “There are a lot of enthusiastic people who have been out of electronics for 20 years, but now they are back and having a great time again.”
Chip Gracey was fascinated by electronics, even as a child. At just 8 years old, he took apart a calculator and hooked it up to a stereo just to see what would happen. Later, he learned computer programming on an Apple 2 computer his dad would bring home from work.
After high school, he half-heartedly attended three semesters at American River College, but felt he was wasting precious time. In 1987, his 0.95 GPA and the resulting academic probation ended his college stint, so he launched an electronics company out of his parents’ home in Carmichael.
Today, at Parallax’s 20,000-square-foot facility, its 44 employees design and make a cache of robots fly, roll and walk. Elev8, an unmanned aerial vehicle, flies and can be used for aerial photography, among other things. Employees also create educational materials for teachers and hobbyists and program microcontroller chips.
Microsoft partnered with Parallax about 10 months ago to create a robot that can be programmed by its users to do common household tasks. In the past few months, Parallax has sold more than 100 of these robots for more than $1,000 each and expects Microsoft to buy five times as many this year.
Parallax has excelled due to persistence, ingenuity and plugging all profits back into the company for future product development. Because they own the company and don’t owe venture capitalists a dime, the Graceys have full power to create new products and further grow Parallax’s customer service and engineering support without regard for stockholders.
Avoiding the venture capital funding route has been difficult, because it takes years to design and fabricate a microcontroller chip; it took eight to develop Propeller 1 and six years for Propeller 2. Salaries must be paid, software must be licensed and up-front fabrication costs can add up to hundreds of thousands of dollars before a product is even ready to sell.
“Typically, companies that design chips are very large, and they have venture capital funding,” Ken Gracey says. “We did it on our own firepower. We made $2 and spent $2.”
Aside from creating innovative products and being financially responsible, Ken Gracey says Parallax is thriving because of its dedicated employees.
“Fun and freedom is a big part of our company,” Ken Gracey says. “To keep and support a productive staff, it’s important to encourage them and to give them freedom to really run the place the way they want to.”
Recommended For You
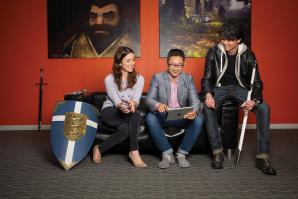
Mind Games
Tech darling Mark Otero hit it big, then almost hit restart
Bright orange walls and ergonomic chairs. A black conference table flanked by a half-dozen scruffy-chic men (zip-front sweaters, double-pierced ears, turn-of-the-millennium tattoos) and three times as many digital devices (nobody brought just one).
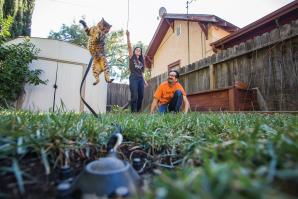
Start Me Up
Local residents make product dreams a reality
Salon owner Carol Milani had never invented anything before, but she needed a way to keep her strong and fearless Bengal cat from escaping the yard.