Lance Hastings became president and CEO of the California Manufacturers & Technology Association in November 2018. Founded in 1918, the Sacramento-based trade organization represents 400 businesses in the manufacturing sector, which employs more than 1.3 million people and generates roughly $288 billion annually. Comstock’s spoke with Hastings about challenges faced by manufacturers and how CMTA works to improve the business climate.
What is the biggest challenge faced by manufacturers in California?
The biggest challenge we’re facing is a workforce issue in that we have a silver tsunami coming, particularly hitting our sector harder than most. Because when you come into manufacturing, you tend to work in the role probably 25-30 years, you end up retiring from the same entity. So we have a large (number) of those retirements coming due in the next five years, and the concern is, are there going to be enough skilled employees of any age to take over those roles? Right now, manufacturers (are saying) they don’t really see that replacement population skilled enough, ready enough or desiring to work in the manufacturing sector. That is the day-to-day challenge that I hear the most from our members. In order for us to be a trade association for manufacturers, we really have to address that with the Legislature and others to look for ways and programs to help build a skilled workforce.
How is CMTA working with the Legislature to address this challenge?
We work with the Legislature to secure (what) are now called career technical education, CTE, funds. It’s an evolution from what we used to know as vocational education in high schools, more trade school education, and the key word is “career.” Yes, there is a technical component and skill, but it’s for a career. The Legislature and (Gov. Gavin Newsom’s) administration have been very open to that concept. The challenge that we all face is acknowledging that the subsequent generations have different work habits and expectations about working. I’ve been using the millennial as an example; 2-3 year timeframes is what we’ve seen they like to operate within (for a job), and that would mean we would have to train 10 employees every three years to get that one 30-year employee, just as a conversion factor. … It’s not really an easy thing to get your hands around. We’re going to need to fill 1 million jobs at some point here in the (near) future.
How is CMTA working with universities or high schools to develop career technical education?
Every first Friday of October is national Manufacturing Day, where we invite manufacturers to open their doors to the community to have people come in and see what the fuss is all about. … What we’ve seen … is children of school age get really excited about manufacturing — they see machinery, they see people making things. But in so many cases I’ve heard anecdotally, their parents would say, “Well, you don’t really want to work here.” Because there’s a notion about manufacturing that it’s dirty, dark and dangerous. And we’re having to correct that. So that’s at the younger age. Knowing we have this dynamic going on, I approached Sacramento State … to establish a focus on manufacturing with the long-term intent of establishing a manufacturing institute at the university that bridges academic and engineering and business to really promote manufacturing as a profession for people of all skill levels. It’s not just your MBAs that are going to be the chief financial officers, or your engineers who are going to be the head of engineering, but everybody can have a good career in manufacturing. Next summer, we will be providing a curriculum for (Sac State’s) summer academies for high school students; they’re adding manufacturing as one of the one-week courses.
Are energy costs a big challenge for manufacturers in California?
Energy costs and reliability are the second biggest issue facing manufacturers, because we rely so heavily upon the energy inputs. Most Californians wouldn’t realize that 30-40 percent of the costs of a manufacturing facility are tied up in energy. They’d probably assume it’s 10 percent, not too unlike a home. But it takes a lot of energy to make things. With the outages we’ve had — the public safety power shut-offs — the lead time for a manufacturer is far greater than a 24-hour notice or whatever a utility is able to provide. It’s just not enough. When we get a notice that there may be a shutdown, we essentially have to shut down because it takes 48 hours or so to properly shut down a manufacturing facility. And it takes about 48 hours to get it back up and running. So if you’re a manufacturing facility in an area that’s had some shut-offs, you’re down for a four-day minimum, and that’s very difficult to respond to because you may have some process in the middle, and if it’s a perishable product, you’ll lose that, and if it’s not perishable, like cement, it can clog up your entire operation. (This leads to the) discussion of what about generating on-site energy? Most on-site generation is either gas-fired turbine or diesel generator, and the air districts will not permit those — so wrapped up in all of this is a regulatory scheme that is challenging, especially for manufacturers, and — no surprise — we’ve had several leave the state to go other places.
What are some practical ways the energy challenge can be addressed?
I have a three-legged approach to the solution. That would be to fix the infrastructure, fix the wires, fix the forests, because the (California Public Utilities Commission) testified at a hearing this year that 90 percent or so of the fires caused by electrical wires are from vegetation failure hitting the lines, breaking the lines. And then the liability: If a utility is looking at a liability scheme that it’s better for them to turn off the power than to leave it on, it’s kind of a backward paradigm. When I was taking on this role a year ago, I was living in Virginia, I read the newspaper and it said, “California due to shut off power due to high winds,” and I couldn’t believe what I was reading. … So I knew the situation was dire. I arrived and started my job on Nov. 12 (2018), so during the Paradise fire, and it was a very quick lesson in the challenges facing the infrastructure of California … the roads, the water, the electric grid, the movement of goods and services through roads or intermodal. The infrastructure in California really needs some attention.
You’ve spoken about changing the narrative around manufacturing. How does that happen?
If you walked into a manufacturing facility today, you would be surprised at the cleanliness, the quietness and efficiency. Because how Hollywood portrays manufacturing in order to meet their narrative and to tell their story is not something that matches up to reality. One of our largest members is Tesla. They make cars. I did a tour (at Tesla’s Fremont factory) in March (2019), and it was one of the quietest facilities I’ve ever been in, and they’re stamping metal into doors and hoods and assembling cars. That struck me. Here’s a manufacturing facility that people on the outside will think, “Oh, I know what’s going on in there,” and they don’t. They have an idea but not that real experience. I think when more Californians get in touch with manufacturing as a sector and its contributions to the economy, there will be an added appreciation, which helps change the narrative. Half of what our lobbying team does is put a face on the manufacturing sector for legislators and the governor’s administration, and I think that’s the best thing we can do.
What is your association doing to encourage manufacturers to stay or expand in California rather than leave?
That’s where our lobbying team really comes into play by making sure the environment in California for manufacturing is improved. We have some regions that are more important — and focus areas — than others, namely the Central Valley. We have so many people — tens of thousands every day — driving from the Central Valley to a manufacturing facility on the inland side of the mountains to cities like Fremont, Santa Clara, Oakland and even San Francisco, which is harmful to the roads, to the environment through auto emissions, and just not good for their quality of life, spending six hours a day in a car. And moving some of those facilities to the Central Valley and bringing the jobs closer to where the people are choosing to live and (where it) is much more affordable … focusing on opportunities like that make a lot of sense for us.
How is automation affecting manufacturing, and how do you expect it will affect this sector moving forward?
Automation is really another word for efficiency. A great example: The (California) Air Resources Board was at a hearing that I was at, and they offered information that California’s (manufacturing) output had increased and emissions had stayed the same, and they observed correctly that it’s all about efficiency. Hollywood again owns this narrative that automation is replacing people, with artificial intelligence being one of the things referenced a lot. But the machines need to be managed (and) serviced by humans, and there will always be opportunities in that space. It is not just about job displacement, as a lot of folks would believe. It may be about job retraining and alignment.
Gov. Newsom appointed you to the Future of Work Commission. Can you tell me more about this commission?
There’s 21 of us from varying backgrounds and experiences, and the objective is to really take a forward look to what the future of work is going to look like, from both an employer and an employee standpoint. I had approached the administration soon after taking this role, saying that I was growing more and more concerned about what the future of work would look like in the manufacturing sector, that if we have an employer who had misaligned expectations of a future employee, that would be a problem for the industry — whether it’s a millennial or Gen X … employee that everyone’s expectations would be met. … If everyone is misaligned, that would impact our sector very greatly. It’s in that vein that I’m participating in this (commission). … We’re (more than) halfway done with our work. We’ll have a draft report out in May. It could be the roadmap for the Legislature, the administration, employers and employees for several years to come.
Recommended For You
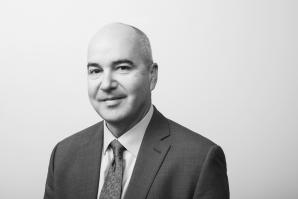
A City’s Growth Spurt
City of Lincoln Economic Development Manager Shawn Tillman on growing business and revitalizing downtown
Economic Development Manager for the City of Lincoln Shawn Tillman discusses growth, industry and foreign trade.
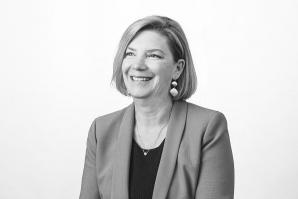
Marshall Medical Center CEO Discusses Health Care for Rural Residents
Comstock’s spoke to Marshall Medical Center CEO Siri Nelson about her organization’s efforts to provide quality health care services to residents of El Dorado County.
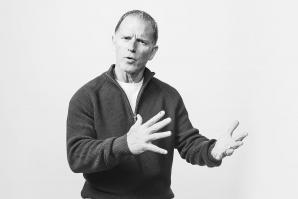
Risk Management
HaneyBiz CEO Mark Haney on advice for investors and entrepreneurs
Mark Haney, the entrepreneur, angel investor, radio host and CEO of Rocklin-based HaneyBiz, says investors should look for startup founders who work well together and are committed to the product.
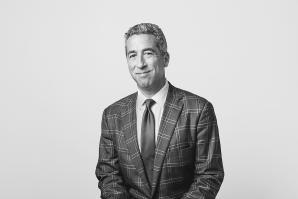
The Defenders of Small Business
John Kabateck on the myriad challenges facing Main Street, USA
John Kabateck of the National Federation of Independent Business speaks to Comstock’s about tax issues affecting business in California and his organization’s position on Assembly Bill 5.