The construction site was nearly immaculate. There were no free-standing ladders, power cords were coiled neatly and only a stray nail, crushed cup and small pile of sawdust littered the floor. The 91,000-square-foot factory was full of skylights with chartreuse buttresses and turquoise shelving, creating a bright, showroom feel.
Signs announced each of the 22 workstations at Zeta Communities, a builder of modular construction. The four-year-old San Francisco-based company opened a factory at McClellan Business Park in 2009, hoping to transform the construction industry.
Zeta, which stands for zero-energy technology and architecture, builds net-zero energy and energy-efficient â?¨single-family and multifamily homes, commercial buildings and classrooms inside its factory, rather than onsite, and delivers them throughout the West.
Net-zero energy has several definitions, but Zeta follows one provided by the U.S. Department of Energy: A building that produces the same amount of energy it consumes over a year. Zeta’s baseline building is 20 percent to 33 percent more energy-efficient than Title 24 standards, and its net-zero energy building exceeds the regulation by 40 to 58 percent. According to the Department of Energy, buildings consume 40 percent of the nation’s energy and 73 percent of its electricity while generating 39 percent of carbon emissions.
Zeta’s goal is to become a nationwide producer of modular net-zero energy and energy-efficient homes and commercial buildings. Its three founders started the company to help address climate change, curtail buildings’ production of carbon emissions and reduce the consumption of natural resources and energy during construction and a building’s lifetime.
The company, funded by private equity and venture capital financing, started during the housing downturn. While the recession has limited the number of projects Zeta can build, its founders believe it will be a boon.
“Actually, it’s a good time to open a company that wants to make an impact on the industry in terms of changing basic assumptions and methods,” says Zeta CEO and President Naomi Porat, a company co-founder. “In this period, our clients — developers, builders, architects — actually are slow and have time to reflect on building methods, the industry, where they want to go, how they will reposition themselves in the recovery.”
Zeta employs about 35 people in its factory and corporate offices in San Francisco, Irvine and Washington state. It plans to expand its McClellan work force to 200 and is considering opening factories in Southern California, the Pacific Northwest and Colorado during the next few years. As of April, the company had completed 11 buildings but can produce the equivalent of 500 houses annually.
“The idea is to replicate this model nationwide so that we can scale affordable, energy-efficient and net-zero energy buildings across the country,” says Shilpa Sankaran, a co-founder and vice president of marketing and communications. “The entire model is based on no price penalty.”
Building green using conventional techniques, Sankaran says, costs 15 to 30 percent more than standard construction, mostly because of the higher cost of green building materials. For Zeta to make its costs equal to those of standard construction, it needed to reduce other costs such as time, construction financing and labor.
Zeta is able to cut construction time by up to 70 percent, costs by 15 to 20 percent and generate 80 percent less waste than conventional site-built construction, its founders say. It does that through efficiencies, including buying materials in bulk and using parallel processing, a construction method that splits building into two lines. On one line, components such as floors or walls are built in two hours. Then the building moves down a separate line where each component is installed.
Buildings can be built in as little as a week. Indoor construction saves money because there are no weather delays, and it allows clients to complete site work, such as grading and laying foundations, simultaneously. The finished building is trucked in parts and assembled on site, typically within a few hours. The final work generally takes a few weeks and may involve installing elements such as solar panels and carpeting.
Tierra Pacifica, a Santa Cruz charter school, plans to install a Zeta-built portable classroom in June, says Nga Trinh-Halperin, the school’s development director. San Jose-based Vuma designed the classroom. Tierra Pacifica parents and staff wanted a builder that embraces eco-stewardship to model the values they’re teaching the children, Trinh-Halperin says.
The 960-square-foot classroom will have solar panels and be at least 30 percent more energy-efficient than Title 24 standards. It will have interior lights that automatically adjust to sunlight, recycled carpet and a rainwater harvest system for outside plants.
Vuma’s founders have extensive experience working with modular school manufacturers throughout California and chose Zeta to build its design because of its willingness to innovate, says Vuma President Ralph le Roux.
Children perform better in classrooms with high ceilings, le Roux says, but most modular manufacturers would have built a solid, flat roof to allow for easy transport. Zeta agreed to a custom solution: a skylight-embedded elevated roof attached on site.
While net-zero energy buildings remain a niche, several construction experts say consumer demand and policies at the state and national levels encouraging their construction in the commercial and residential sectors will help push them toward the mainstream.
Dave Hewitt, executive director of the New Buildings Institute, a Vancouver, Wash.-based nonprofit, says net-zero energy buildings have an inherent marketability. “These buildings are going to be perceived as the leading edge of the next wave of construction,” he says.
Recommended For You
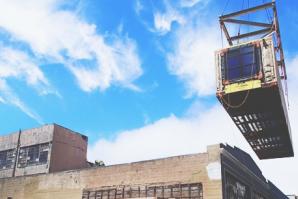
Putting the Fab in Pre-Fab
Modular construction cuts construction and energy costs
The final stages of construction at a trend-setting apartment project in San Francisco’s SoMa neighborhood, known by its address at 38 Harriett St., largely resembled a life-sized game of Tetris.
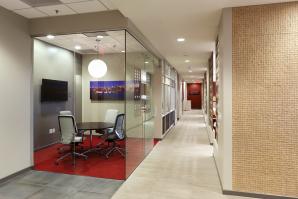
Farewell to the Corner Office
The next generation of workpace design
Walk into any coffee shop and it’s obvious that the place we call “the office” has changed. Many of the people sitting at tables are likely mixing laptops with lattes as they browse email and write reports. Some may be pitching a sale over coffee.