Like an oil derrick with arms, the school-bus-yellow robot is the center of attraction in an otherwise colorless room dominated by metal castings and concrete floors. Moving like a mime on a street corner, the robot picks up a metal casting, holds it to a computer-run camera and then places the part and the fixture that holds it on a machine for tooling.
The ultimate product will be larger than a typical car and weigh more than a couple multi-ton trucks. But at the Mori Seiki manufacturing plant outside Davis, practically every modern convenience, including products as small as toasters and cell phones, begins to take shape.
This is ground zero in the world of manufacturing, the place where machines make parts to make other machines, says Adam Hansel, a chief technical officer at Mori Seiki. The company’s $50 million investment, operating at about one-third capacity, is one of the newest bright spots in an economic sector that has been losing ground throughout California. It also is indicative of future manufacturing growth that is more about software than smokestacks.
The Sacramento Area Commerce and Trade Organization (SACTO) estimates that manufacturing represents 4.1 percent of regional employment. Those 34,800 jobs are far fewer than the 48,200 of a decade ago. The California Manufacturers and Technology Association contends the state is losing manufacturing jobs at a faster clip than the rest of the country due to costs. Nationally, manufacturing output increased 4.4 percent since 2010, while California’s growth has been stagnant at 0.4 percent, according to Geno DiCaro, the association’s vice president of communications.
“California is dead last among the states and is dropping off investor lists when it comes to manufacturing,” DiCaro says. He cites a list of reasons, including energy that’s twice as expensive as the national average due to renewable energy mandates, high workers’ compensation rates and the state’s greenhouse gas emission rules.
SACTO’s Bob Burris concedes that stats about production output and jobs are “sobering” but contends they mask the real nature of the region’s manufacturing. “When you see the types of jobs, you see less assembly and more higher-level jobs in engineering and design,” he says. “Those are the kind of jobs you want because they are longer lasting and create a bigger impact in the region.”
Manufacturing anchored in research and development works well for small and mid-sized companies because, unlike industries such as auto assembly, they are constantly changing products to meet customer demands or market conditions. “I think California is a strong market for that, and our universities are the No. 1 reason,” Burris says.
Mori Seiki is a shining example.
The Japanese company has a dozen sales and distribution offices throughout the U.S. and Canada, but the Davis facility is Mori Seiki’s first manufacturing plant in this country. Opened last July, it gives the company a base from which to reach customers in one of its biggest markets.
The 100 or so “cutting” machines the company turns out each month end up in all corners of the U.S. “We have a lot of aerospace customers in Los Angeles and the Pacific Northwest, energy producers in Houston and the automobile industry in the Midwest,” says Chief Operations Officer Adam Hansel. Computer chip makers in Silicon Valley and dental equipment manufacturers in the Bay area also are customers; a Mori Seiki customer in Richmond uses the machines to manufacture high-resolution optical measuring devices.
“The factory is here so we can be close to our customers,” Hansel says. “There are benefits to talking to the customer directly, getting to the heart of a matter and fixing it. The speed of business these days is the speed of communication.”
The factory’s location was very much intentional, the evolution of a research and development operation created by Hansel in 2000 after he graduated from UC Davis with a degree in mechanical engineering.
Burris noted that much of the region’s recent manufacturing growth has been tied to ag research through UC Davis and spin-offs from the computer industry. Bayer CropScience for example, will soon open a new facility in Yolo County, joining Nippon Shokken, an Asian manufacturer of gourmet sauces. Both take advantage of skilled researchers, engineers and scientists who work alongside automated production technology.
“Any company that uses automation to eliminate jobs and reduce overhead will die here,” Hansel contends. He uses robots for the mundane tasks since most of the 140 Mori Seiki employees are mechanical, electrical or software engineers. The use of robots and automation frees them for more valuable jobs, such as developing hardware and software solutions to complex manufacturing problems. Additionally, automation gives way to human artistry in final assembly when technicians use electronic hand tools to measure tolerances that are one-twentieth the width of a human hair.
“When you’re dealing in microns, it takes a skill that is almost an art and not something you can learn from a manual,” Hansel says.
That same combination of mechanics and brainpower is what kept Art Armstrong Jr. afloat through the worst downturn his family-owned business has seen in its 50 years. In a climate-controlled building near the Auburn Airport, Armstrong Technologies turns out small numbers of R&D parts for the medical, aerospace and defense industries that range from robotic arms for operating rooms to casings for sophisticated weapons, such as infrared night vision equipment and experimental fuel nozzles for rockets.
“We specialize in close tolerance, high-tech products,” says the second-generation businessman. “We take on tough-to-build projects that companies don’t want to take overseas.” The delicate nature of Armstrong’s projects is evident when you hit the front door. Only U.S. citizens can sign the log and get past the receptionist.
Like Hansel, Armstrong emphasizes that, while technology can make some tasks easier and reduce the chances of making costly mistakes, the skill of craftsmen who can fabricate parts from exotic materials, such as high grade steel or titanium, is still essential in manufacturing.
What begins as a block of forged aluminum, for example, still must be turned into a part that separates whole blood from platelets with the same artistic eye and patience that a jeweler sees when cutting a diamond. “It takes a certain type of person to do this work well,” says Armstrong. “You can only do this so fast, and it’s like doing surgery on metal,” he adds. “This is high-technology material, and these parts are not cheap. A mistake can be very costly.”
The last stop for any finished part, whether it’s a rocket fuel nozzle or a robotic surgical arm, is quality control. A lone operator sits in front of a bank of computer screens in the spot Armstrong calls “the most important room in the building.” A table holding a pallet of finished material is leveled by a laser for precision. A rotating Reneshaw probe touches each piece in dozens of places, recording measurements in a computer to ensure they are within specifications. The quality check takes minutes. In an earlier era with hand-held tools, the job would have taken hours. “You have to sweat the details,” which in this case calculate profit or loss ten-thousands of an inch at a time, Armstrong says.
As a survivor in a manufacturing industry littered with casualties, Armstrong believes mass production will not return to its boom days any time soon. But by spreading his business among many industries, he believes he is better prepared for what comes in the next era. “You can never be too diversified,” says Armstrong, who is checking into whether the oil and gas industry can use a good lubricating pump.
Recommended For You
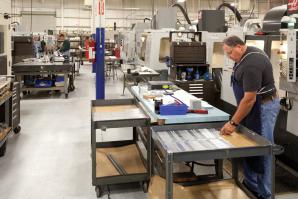
The Auburn Advantage
How one city turned lifestyle into business leads
Downtown Auburn has a distinct, modern-day Mayberry feel, from the stone-paved sidewalks to the rustic brick bus stop. But five miles away,
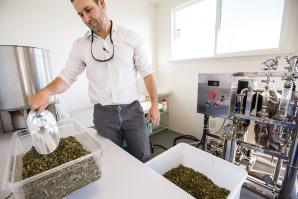
Sugar & Splice
The Capital Region offers everything nice for ag-bio companies like Stevia First
A Capital Region startup is striving to be among the first in the nation to produce the zero-calorie, natural sweetener stevia on an industrial scale. An agricultural biotech company, Yuba City-based Stevia First is bolstering its chances of success by actively collaborating with experts in the field, drawing on the area’s robust talent pool of farmers, agronomists, agricultural innovators and biotech experts to develop a product that’s superior in both taste and cost compared to its foreign competitors.